Can a fidget-sized cube transform tedious time reporting?
This is exactly the type of creative, impactful question we want team members to explore in the Nansen Product Lab. Our new internal-transformation initiative, the Product Lab was created to allow participants to flex and strengthen the muscles of rapid innovation and practice executing on ideas—and specifically ideas separate from day-to-day Nansen client work and deliverables.
The first three-person team to complete the Product Lab Design Sprint dreamed up a platform that would marry the functionalities of LinkedIn and Tinder, and ended up building a prototype for a “lunch picker” app that delighted users who tested it. A few weeks later, it was time for a new group to enter the Nansen Product Lab.
Meet the team: Nansen Product Lab, Rotation Two
A diverse team composed of Nansen partner and co-owner Arnold, senior developer Alan, and junior developer Hyesoo, Rotation Two embraced the same blue-sky mindset as did the cohort before them.
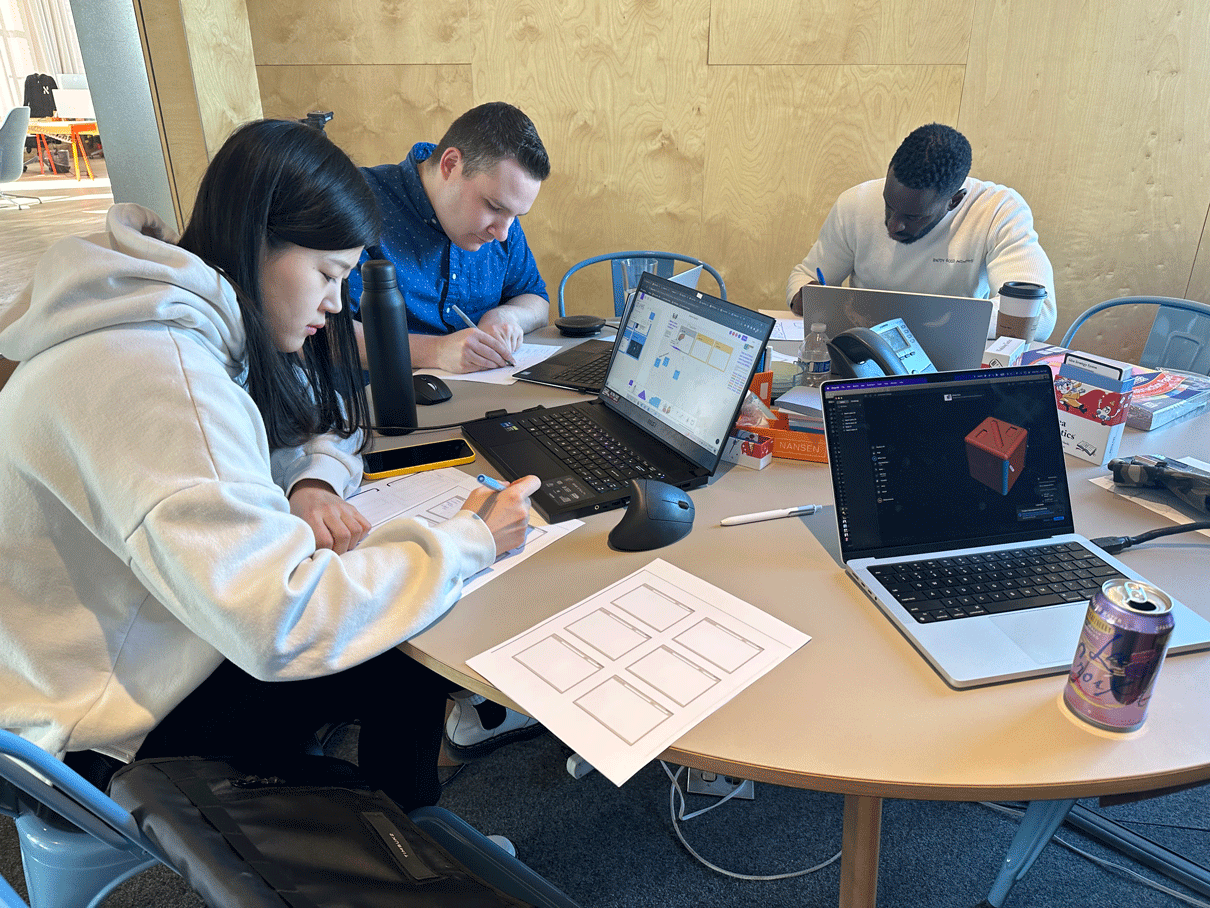
This second team had a unique goal for their Product Lab week, however. They wanted to deprioritize coding and app design in favor of creating something tangible, a physical product. So when the subject of time tracking and logging hours came up as a problem to solve on Day One of the design sprint, they had a spark of inspiration.
By the testing phase on Day Five, the Rotation Two team had 3-D printed a die-shaped cube that could sync with an app (which they also built) to allow users to seamlessly switch between client projects as they tracked hours throughout the workday. Here’s how they did it…
Day One: What do we want to create?
The beginning of the design sprint process calls for a day of exploration, where ideas are raised and discussed.
It seems likely that one of the Rotation Two team members had recently done battle with tedious time-tracking software, or had to dig back through paper trails and memories to complete a detailed client invoice. Whatever the inspiration, it didn’t take long for the new cohort to land on their area of focus: finding a better way to do time reporting at Nansen.
Anyone who has been responsible for tracking and reporting hours for multiple clients at once can tell you that it’s not very fun. Great software exists to help, but even with such tools, time tracking is very manual, can feel counterintuitive, and can hinder efforts towards efficiency.
As part of the Explore phase of their design sprint, Arnold, Alan, and Hyesoo dove into research. What they found was an enticing whitespace to explore, between two sets of existing tools: those for tracking time on the one hand, and those for logging hours and invoicing on the other.
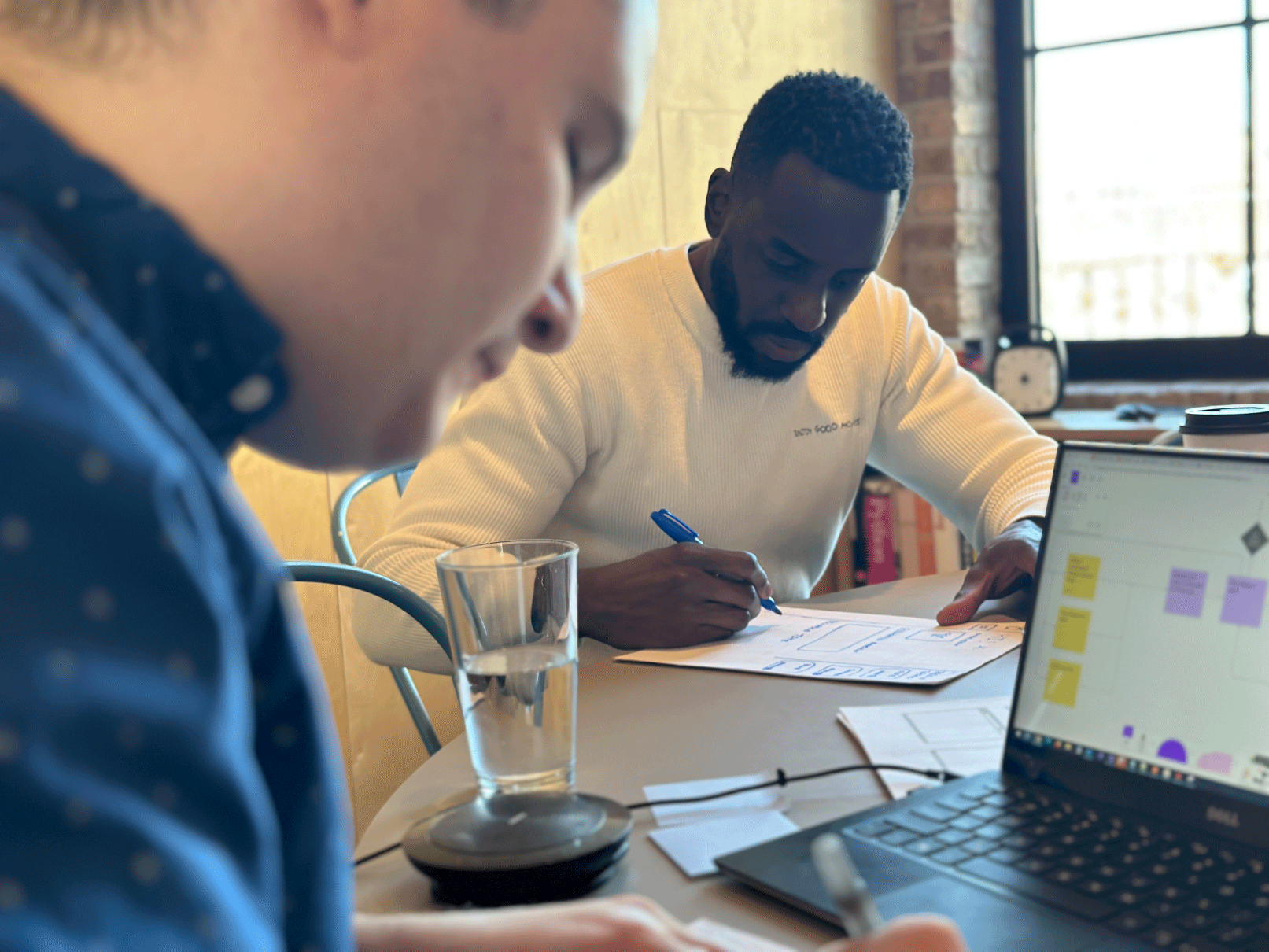
The team had landed on a solution to pursue. They decided to design a physical object to bridge the space between time-tracking and time-reporting tools, a kind of “middleware” solution that could work as an add-on to companies’ existing software and processes.
Day Two: How might we achieve our goals?
Returning to the Nansen Product Lab, the Rotation Two cohort knew that they wanted to design and build a cube or a die that would function as a “dial” of sorts, with each side of the die representing a different client project. They wanted users to be able to flip the object and somehow activate it as a way to initiate hours tracking for a specific project, rather than having to re-open a software program, click around, and type in details every time.
Day Two of the Product Lab Design Sprint is all about making big decisions, quickly and efficiently, about the concept and prototype the team will focus on. Arnold, Alan, and Hyesoo would need to answer a number of key questions to keep their sprint process moving, including:
- What is the overall user journey? How does the die bridge the gap between tracking hours and recording that data?
- What are some of the “blockers” or challenges that this solution would need to overcome, and how might those inspire features and inform the design?
- What key functionalities would the team focus on building during the remaining few days of their sprint?
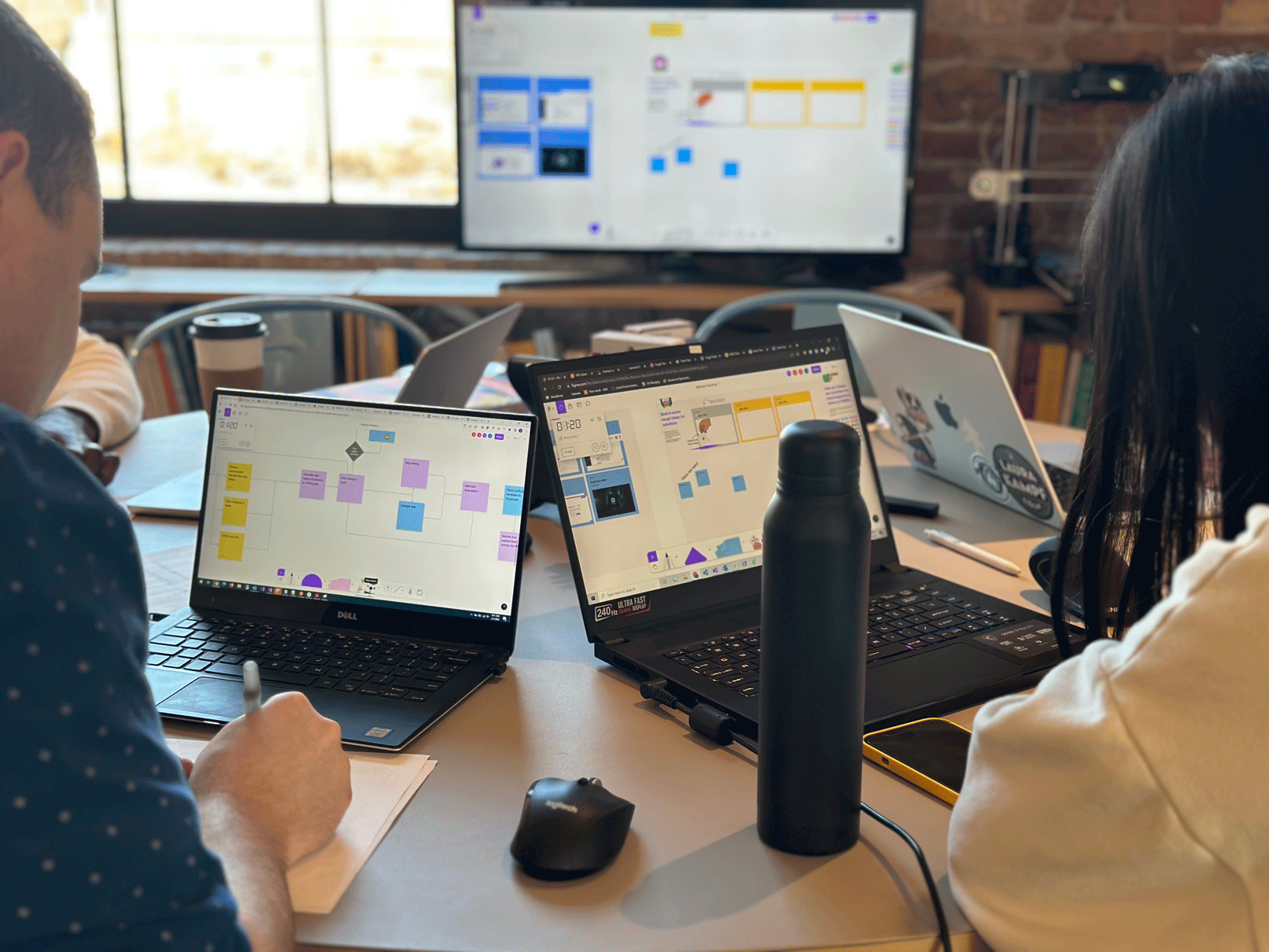
Working together in Figma, the Rotation Two cohort explored these questions, use cases for their die, and some initial workflows. By the end of the day, they had nailed down their plans.
Day Three: What will it look like and how will we build it?
On Day Two, Arnold, Alan, and Hyesoo had defined two key users for their time-tracking die: first, the employee who logs time, and second, the project manager or account manager who reviews the reports. Moving into the Sketch phase of their sprint, on Day Three the team started by building out the workflows for their users.
They also started outlining plans for the key functionalities they would work to create by the end of the week:
- Configuring the physical die, and how it would start and stop tasks
- The app, synced with the cube, which the user would download to their phone
- A dashboard view showing how the data captured by the die would appear
Then it was time to build.
Days Four and Five: Let’s build a prototype
The Rotation Two cohort wanted to be able to truly test and validate their concept by the end of their Product Lab week—and the only way to do that would be to produce an actual die with interactive capabilities. They worked quickly to design the cube and its underlying technology (specifically, NFC tags), and then it was time to 3-D print!
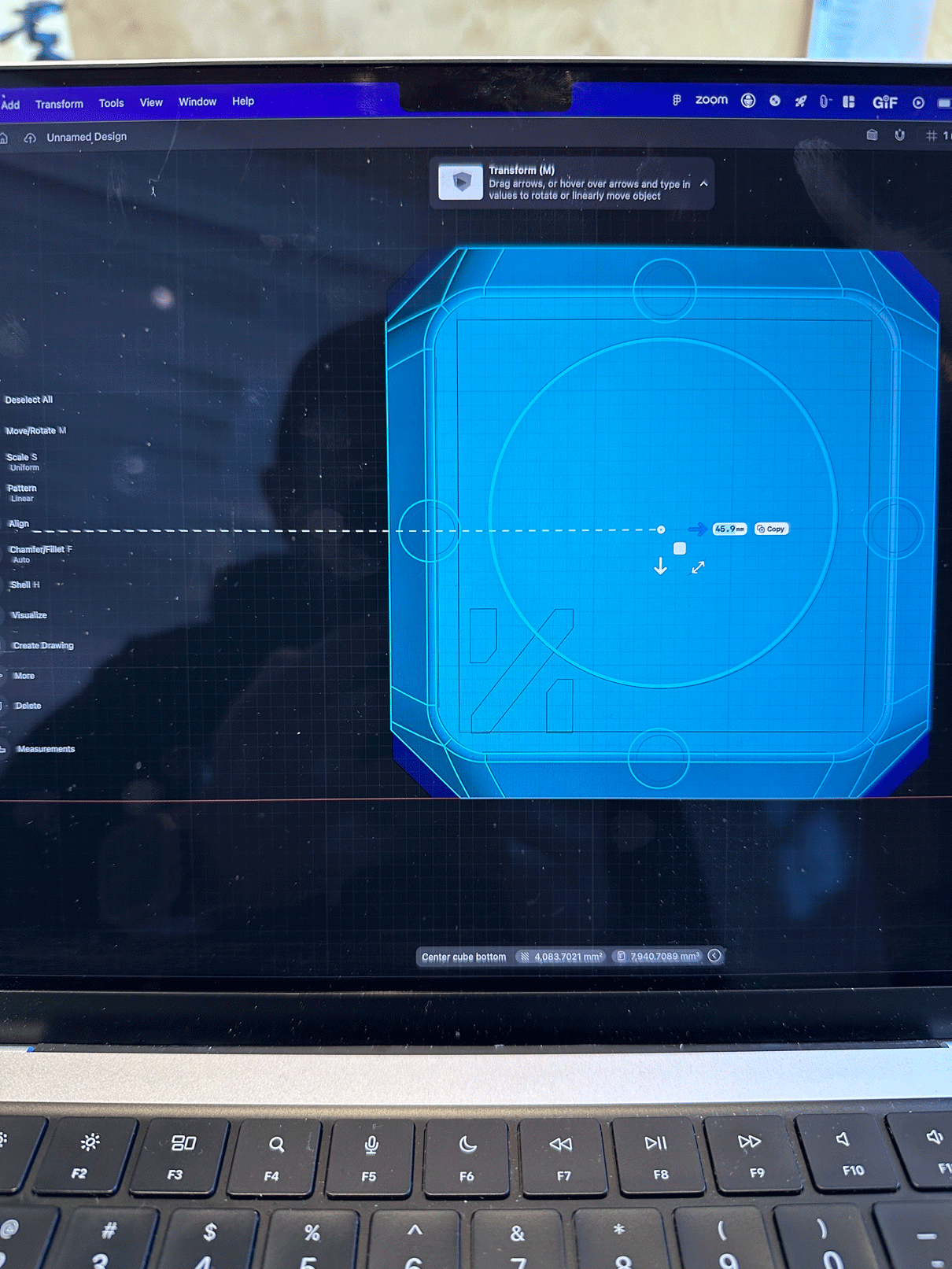
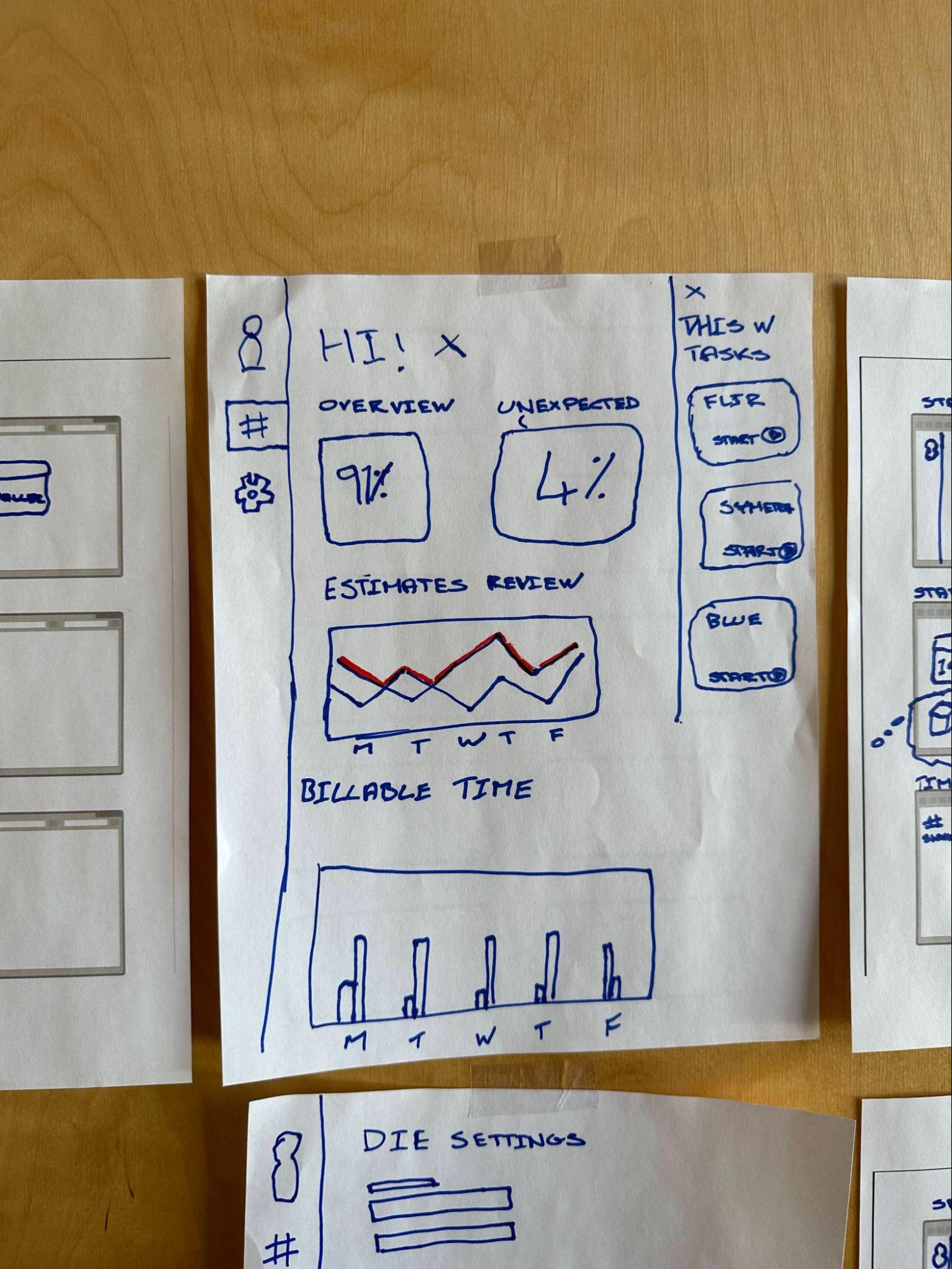
On the app side, the team credits Alan (who is a Nansen senior developer, remember) for the intensive focus he brought to the project. Alan did a ton of coding during the back half of the design sprint to build prototypes for the app and the time-tracking dashboard view. In the end, he was able to build an integration with Toggl for time tracking and Workbook for invoicing – so the die and app could actually work together in an end-to-end flow!
There were of course many ideas for their time-tracking die that Arnold, Alan, and Hyesoo simply didn’t have time to complete during the five-day design sprint, including experimenting with interactive displays on the die and different methods for updating the projects stored therein. But by the end of their Product Lab rotation, the team had achieved their primary objective, and had a working prototype for users to test.
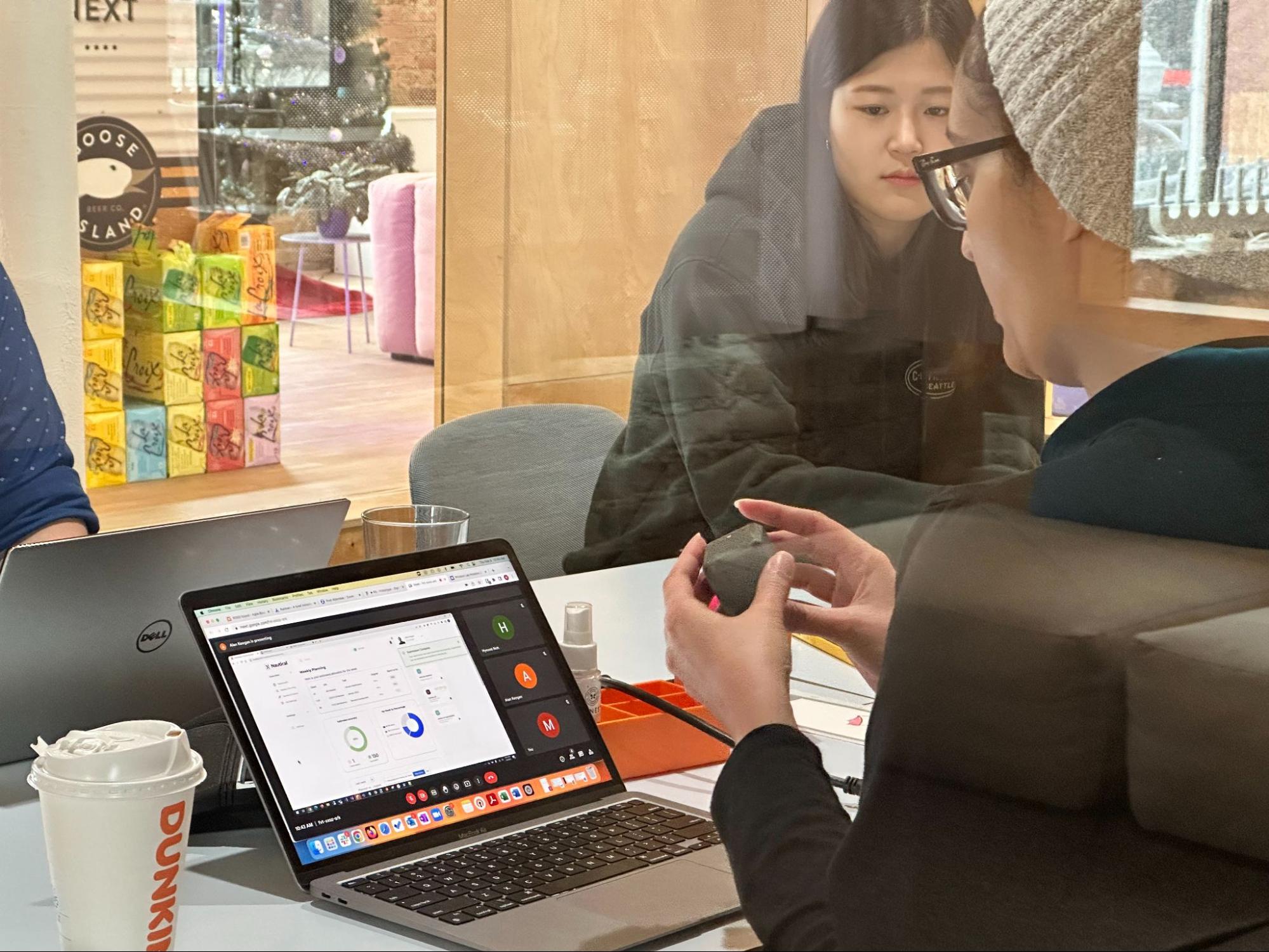
Nansen Nautical: the prototype
Arnold, Alan, and Hyesoo took full advantage of their time in the Nansen Product Lab. Their final product, which they call Nansen Nautical, is a testament to their bold thinking, ambitious goal-setting, and simple hard work.
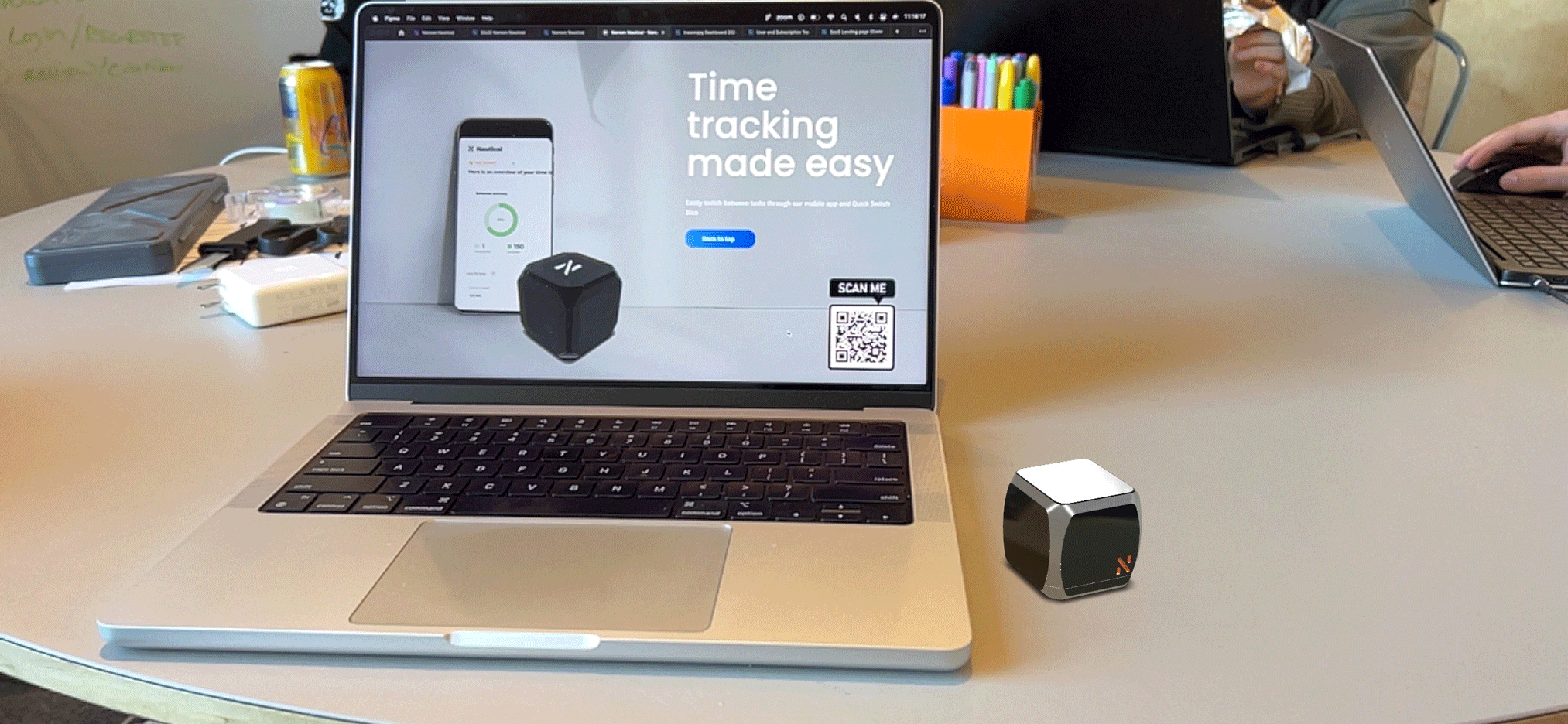
What did the users who tested the prototype have to say about it?
Yes; I think this would be a fun tool for people who don't like documenting/entering time.
I think when working on multiple projects, this could be helpful, the only downside I can see is if you're typically booked on one project (or even two) it wouldn't necessarily be helpful.
100% of users said that this product would make tracking time more easy or accurate.